Description
Replaceable silicon carbide cyclone and hydrocyclone liners are specifically engineered for classifying applications.
Liners are designed for highly abrasive ores processed such as coal, iron ore, gold,copper, cement, phosphate, sand and other hard rock mining.
With a variety of highly abrasion resistant compositions available, Sunny Steel ceramic cyclone and hydrocyclone liners allow for:
- Improved life and performance over urethane, rubber or tiled construction
- Ease of installation
- Accurate and repeatable separation performance
Many products can be made from it such as beams, rollers, cooling air pipes, thermal couple protection tubes, temperature-measuring tubes,sealing parts, and special shaped parts.
What are the advantages of silicon carbide cyclone in coal preparation
Compared with other coal preparation methods, silicon carbide cyclone has its unique advantages, which can be summarized as follows:
- It has the advantages of large processing capacity per unit volume, high separation accuracy and low separation particle size limit, which can be used for raw coal separation with various washability. The unit capacity of cyclone is much higher than other gravity separation equipment.
- Less investment and convenient management. The traditional view is that the dense medium coal preparation system is complex, the equipment wear is serious, the maintenance quantity is large, the management is difficult, the coal preparation cost is high, and so on. However, with the continuous improvement of dense medium coal preparation technology, especially the advent of three product heavy medium cyclone, and the emergence of corresponding auxiliary equipment and reliable wear-resistant materials, the above understanding has fundamentally changed.
- The small size of the plant and the compact and neat layout of the equipment make it convenient for the construction of the coal preparation plant to realize the scale and greatly shorten the construction period of the coal preparation plant.
At present, there are two series silicon carbide products of pressureless sintering silicon carbide (SSIC) and reaction sintering silicon carbide (SISIC), which are widely used in mining, metallurgy, chemical industry, electric power, petroleum, furnace, machinery, steel, energy, environmental protection, building materials, semiconductor, aerospace and other fields. Compared with reaction bonded silicon carbide, pressureless sintered silicon carbide has higher purity, better mechanical properties, more prominent corrosion resistance(Resistant to strong acid and alkali corrosion, It is also the only ceramic material which can resistant to hydrofluoric acid corrosion), higher wear resistance, because of there’s no free silicon in the material. It can be used longer service life in environments which other materials not meet.
Silicon carbide (SiC) is a lightweight ceramic material with high strength properties comparable to diamond. It has excellent thermal conductivity, low thermal expansion, and is resistant to acid corrosion. Silicon carbide is an excellent ceramic material suitable for applications requiring good corrosion resistance and wear resistance.
Silicon carbide is formed in two ways, reaction bonding and sintering. Each forming method greatly affects the end microstructure.
Reaction bonded SiC is made by infiltrating compacts made of mixtures of SiC and carbon with liquid silicon. The silicon reacts with the carbon forming more SiC which bonds the initial SiC particles.
Sintered SiC is produced from pure SiC powder with non-oxide sintering aids. Conventional ceramic forming processes are used and the material is sintered in an inert atmosphere at temperatures up to 2000ºC or higher.
Both forms of silicon carbide (SiC) are highly wear resistant with good mechanical properties, including high temperature strength and thermal shock resistance. Our engineers are always available to best advise you on the strengths and weaknesses of each ceramic for your particular needs.
The crystal structure of the SiC ceramic wear-resistant pipe is similar to that of the diamond tetrahedral structure. It is a compound composed mainly of covalent bonds. Its hardness is high (Mohs 9.3), its performance is stable, and its physical properties are similar to diamond. It is also known as emery. Black silicon carbide crystal Hardness is the second-order material for diamonds. It is mainly used for making abrasives and grinding wheels, and partly for the production of silicon carbide ceramics.
Properties
Silicon carbide (SiC) ceramics have a set of unique physical-chemical properties, such as high hardness and mechanical stability at high temperatures, excellent thermal conductivity and low coefficient of thermal expansion, high resistance to corrosion and oxidation, wide bandgap, and others.
- High hardness (second only to diamond)
- Low density 40% the density of steel – approximately the same as aluminium
- Low porosity
- Good wear resistance in sliding and abrasive environments
- Excellent corrosion resistance in most chemical environments
- Low thermal expansion and high thermal conductivity leading to excellent thermal shock resistance.
Properties of reaction bonded silicon carbide
Reaction Bonded SiC has the lowest cost production technique with a course grain. Reaction Bonded SiC provides somewhat lower hardness and use temperature, but higher thermal conductivity. Reaction bonded silicon carbide has high strength, high hardness, hig abrasion resistance, high temperature resistance, corrosion resistance, good oxidation resistance, good thermal shock resistance, good thermal conductivity, rapid cooling and rapid heat resistance and high temperature creep resistance, etc. It can be made into beam, roller, cooling air pipe, thermocouple protection pipe, temperature measuring pipe, burner nozzle, wear-resisting parts, corrosion-resisting parts, sealing parts and a variety special-shaped structural parts.
Properties of pressureless sintered silicon carbide
Compared with reaction bonded silicon carbide, pressureless sintered silicon carbide has higher purity, better mechanical properties, more prominent corrosion resistance ( Resistantto strong acid and alkali corrosion, It is also the only ceramic material which can resistant to hydrofluoric acid corrosion ), higher wear resistance, because of there’s no free silicon in the material can be used in other materials can not meet the environment, longer service life.
Applications
Silicon carbide (SiC) ceramics have a set of unique physical-chemical properties, such as high hardness and mechanical stability at high temperatures, excellent thermal conductivity and low coefficient of thermal expansion, high resistance to corrosion and oxidation, wide bandgap, and others.
Armor
Sintered Silicon Carbide has demonstrated an excellent performance record as ceramic material in composite armor protection systems. The properties of sintered silicon carbide, such as its high hardness, compressive strength and elastic modulus, provide superior ballistic capability when confronted with high-velocity projectiles. The low specific density of the material makes it suitable in applications where weight requirements are critical.
Heat Exchanger Tubes
Sintered Silicon Carbide tubes are used in shell and tube heat exchangers in the chemical process industry. The tubes used in these applications are often over 4 m in length.
Mechanical Seals
Pumps must operate in an infinite variety of demanding environments. Sintered Silicon Carbide offers a high performance seal face material that has proven successful in such diverse pumping applications as chemical processing, refining, mining and pulp and paper processing. The material provides superior corrosion and abrasion resistance; shock resistance; and low sliding friction against a wide range of mating materials.
Bearings
For state-of-the-art magnetically driven pumps, sintered silicon carbide is particularly suited for thrust and journal bearing components. Excellent corrosion resistance provides optimum performance in many chemical environments. High thermal conductivity minimizes the likelihood of failure due to thermal shock, and its specific strength makes it safe to use at high rotational speeds. Bearing components are usually produced as tight tolerance precision ground parts.
Automotive Components and Seal Faces
Due to their greater resistance to both wear and thermal shock, sintered silicon carbide seal faces for automotive water pumps are replacing seal faces made of materials such as aluminium oxide. In many cases the material has proven more suitable in meeting the performance demands of U.S. and European vehicles – i.e. lasting the lifetime of the vehicle without leaking. These components are manufactured by conventional high volume pressing and injection moulding methods to meet the economic constraints of the application.
Blast and Atomization Nozzles
Sintered Silicon Carbide is probably the most popular ceramic alternative to tungsten carbide for blast nozzle applications. Typically providing long life (50% over WC) due to excellent wear and corrosion resistance. The low wear rate maintains the internal nozzle geometry and provides maximum blasting effectiveness, minimum compressor requirements and reduced downtime due to replacement. Sintered silicon carbide is also about one fifth the weight of Tungsten Carbide, so the blasting operation is also easier for the operator. Nozzles are often produced as semi finished (non-ground) components thereby reducing costs.
Process Industry Valve Applications
The outstanding corrosion resistance of sintered silicon carbide, particularly in acids, makes it an ideal candidate for valve and valve trim applications. Typical demanding applications such as slurry flashing, HF acid handling and rare earth processing use sintered silicon carbide valve components.
Paper Industry Applications
The excellent corrosion and wear resistance of sintered silicon carbide provides hard surfaces that can be machined to smooth, highly polished finishes. These finishes offer low coefficients of friction and compatibility with forming fabrics. Tiles, inserts and palm guides are available in finished and semi-finished forms.
Centrifuge Tiles and Wear Parts
Often used in applications where tungsten carbide and alumina fail to provide optimum lifetime performance.
Semiconductor Production
The benefit of using silicon carbide for semiconductor components includes; the thermal expansion match to silicon, the resistance to wear and chemical corrosion which leads to reduced maintenance and component recycling. The material is well suited as a structural material for low mass silicon wafer handling components and rigid, dimensionally stable platforms due to its lightness in weight and high elastic modulus. Typical applications include vacuum chucks, chemical mechanical polishing blocks, wafer carriers, and thermocouple protection tubes.
Correct use of silicon carbide ceramics
Silicon carbide ceramics are widely used not only in industry, but also in other fields. So, what should be paid attention to when using silicon carbide ceramics?
The hardness of silicon carbide ceramics is very strong, although it does not look as eye-catching as other ceramics, but the use of ornamental ceramics is incomparable. In the process of use, as long as you follow the instructions, there is no need to pay special attention to. Just keep it clean.
If the method used is not correct, the silicon carbide ceramics will be damaged. We can extend its service life by regular maintenance.
Parameter comparison
Silicon carbide (SiC) is a lightweight ceramic material with high strength properties comparable to diamond. It has excellent thermal conductivity, low thermal expansion, and is resistant to acid corrosion. Silicon carbide is an excellent ceramic material suitable for applications requiring good corrosion resistance and wear resistance.
Comparison of parameters of silicon carbide ceramic products of different materials
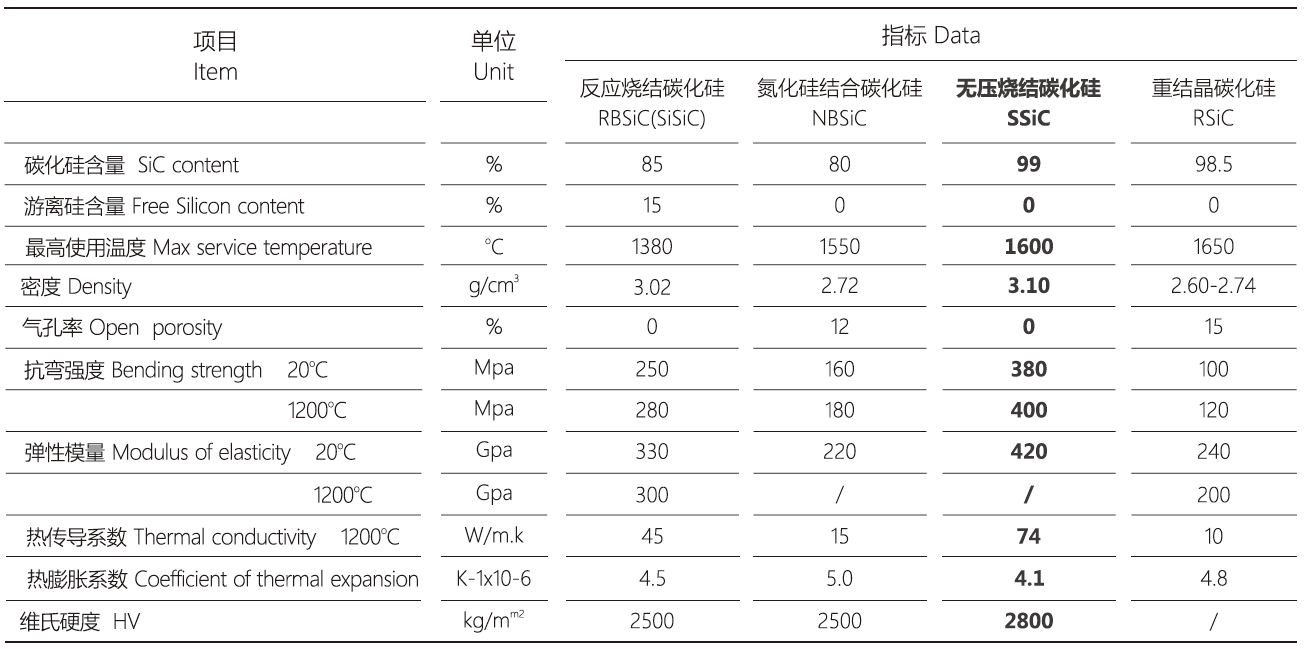
Liquid corrosion test data for different materials
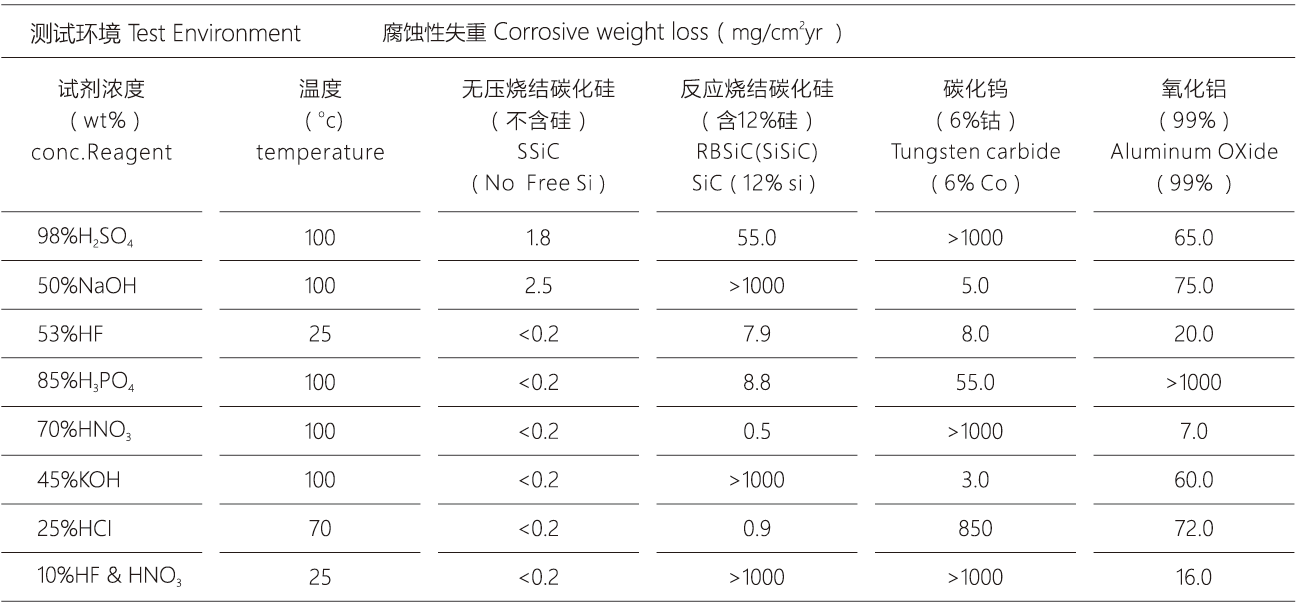
Remarks
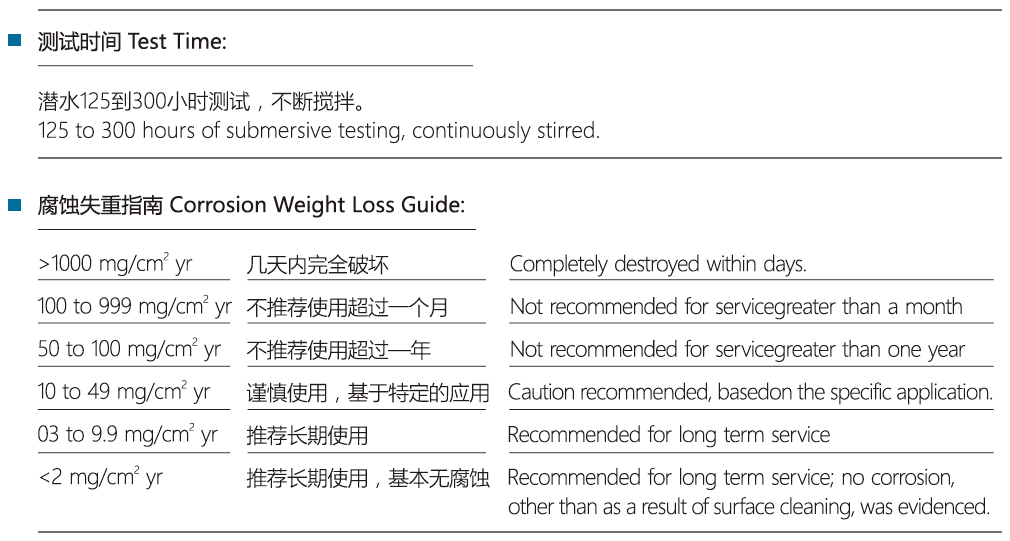
Packing
Our silicon carbide tube and fitting is carefully handled to minimize damage during storage and transportation and to preserve the quality of our products in their original condition. We guarantee intact during transportation, loading and unloading, and have measures to reduce vibration and impact, so as to ensure the integrity of the product during transportation.
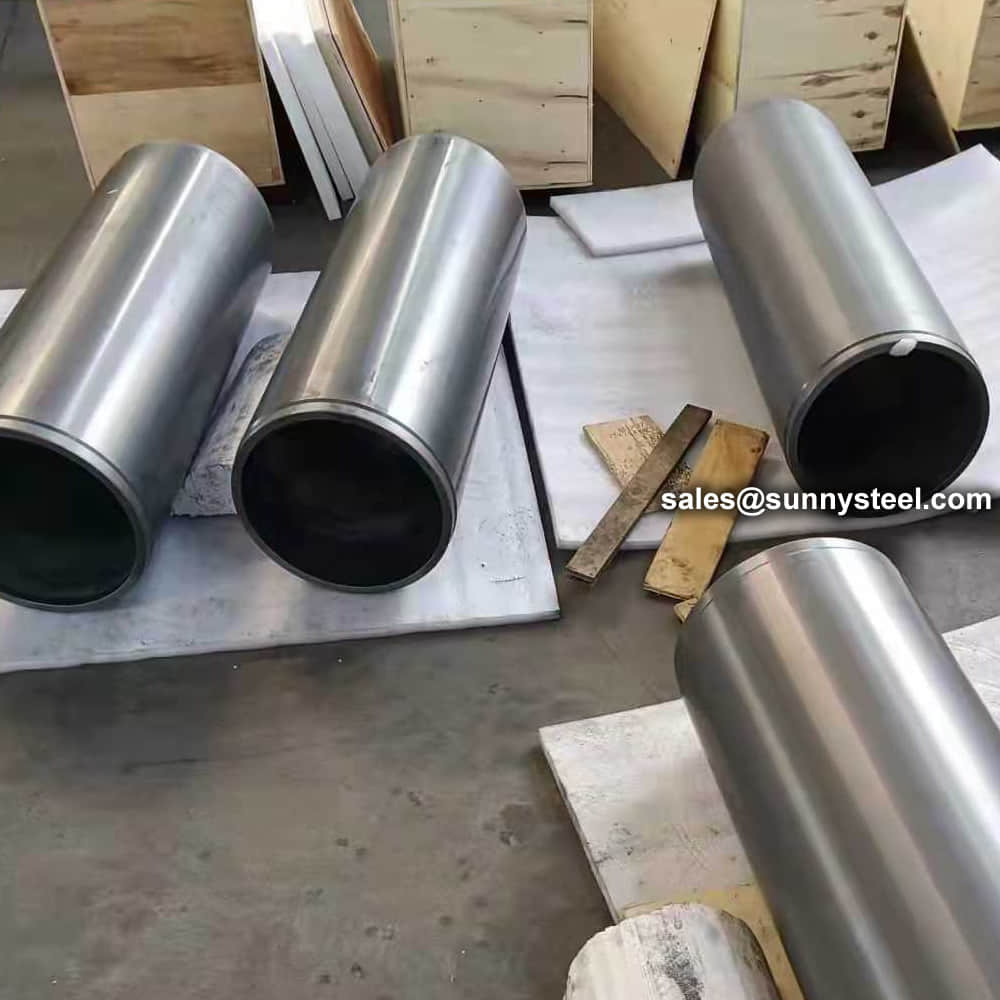
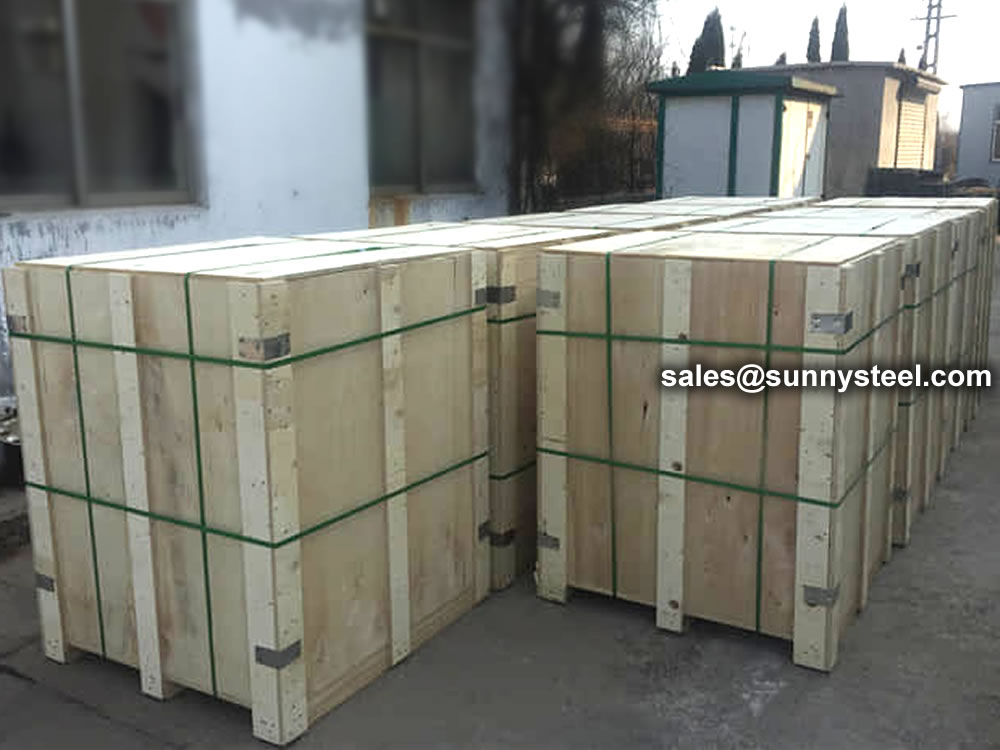
Inquiry
Need to inquire about our products? Fill out the form below and our staff will be in touch!
FAQ
Q: How long is your delivery time?
A: The delivery time of customized products is generally 25 35 days, and non customized products are generally shipped within 24 hours after payment.
Q: Do you provide samples? Is it free?
A: If the value of the sample is low, we will provide it for free, but the freight needs to be paid by the customer. But for some high value samples, we need to charge a fee.
Q: What are your payment terms?
A: T/T 30% as the deposit,The balance payment is paid in full before shipment
Q: What is the packaging and transportation form?
A: Non steaming wooden box and iron frame packaging. Special packaging is available according to customer needs. The transportation is mainly by sea.
Q: What is your minimum order quantity?
A: There is no minimum order quantity requirement. Customized products are tailor made according to the drawings provided by the customer.